robbiethepainter
Super Freak
I just wanted to give some insight into my journey making a trike and then makes some comparisons to Rainman’s figures and possibly others from this board.
I have been working on this trike for about 6 months. I stopped paying attention months ago in the amount of hours. Lets just say a lot. The trick for these kinds of projects is there is often little reference. So for me I start going to period research in hopes to fill in the gaps where the movie still leaves off. This takes a lot of time on its own. Then there is the wonderful trick of taking measurements from the few images that you find so that the proportions can be addressed. I was taking measurements from the stills of Danny and his Mom walking so I could then cross reference to internet information about how tall the actors are. So that I then could determine what the height of the trike might be. I say might, because as you can imagine it all comes down to a guess in the end. Lee wanted the trike so he could then build the figure from it so I had to be sure and get as close as possible. I wanted to make sure these were as detailed and accurate as possible.
Once that is done the actual modeling happens. I opted to use a 3D CAD model because I knew that the objects printed would be more accurate in the end. Lee is brilliant at sculpting things by hand but I am no where near his level of perfection. I started it early on and found the wheel treads impossible to keep consistent. And I figured if I could do the wheels, I could do everything. I also knew that if I was going to ever come close to producing a large number in a short time, there was no way I could fabricate them by hand. This is where the price starts to be affected. If I was going to outsource everything it would make my production time shorter but the out of pocket price would skyrocket. That is why the gurneys are about the same price as these are because I don't have to worry about money paid out just labor. And trust me, I am making about 5 cents an hour for my labor on those. But its ok on those because that was the price I set. But it also has the affect of taking almost two years to finish. Just the metal parts cost nearly half of the price just to have them made and I haven't even added in the production of the plastic parts.
The most of the plastic parts have the luxury of being printed once and then cast but even they come with a per model price. I spent I think $375 for the prints of the plastic parts. The initial price is high because I wanted to get the absolute highest quality because I knew I was going to mold and cast them. Originally I was just going to print everything and avoid the casting costs but the quality for that amount was just too low so I opted this way instead. But the bell is going to be printed for each trike. The reproduction was just going to be too difficult. So the cost of each bell for the trike is little over $10 each. And that is getting a great deal from my printer. The first one was $20. The molding and casting of stuff can get pricey. Its not really affected by size for me, but more the amount of pieces. But I'm sure something like a figure would be much higher in price than the say the pedals. But even still every piece needs to be planned out and tested because to get the best cast, some trial and error has to happen. Im sure Lee’s cast are from a factory, because his castings a perfect. You can see the difference from say me and other board member’s head castings and one of his.
There is one section I was hoping to avoid fabricating but in the end, technology couldn't do it. I think its the main reason Lee wanted me to join him on this project because he could have easily made all the other parts. The frikkn front wheel. I had several different versions attempt printing it which cost me lots to have made, but in the end. it just couldn't be made that way. So I will be fabricating all the spokes and assembling each wheel by hand. The colored trike that Lee has for the prototype took me over 2 hours to make. I think I have the process figured out but still those are going to take some time. If the 30 Lee asked for have to be made, you can do the math and see what that will be like for me.
So as a wrap up, the collectors today expect this kind of attention to detail for this hobby. And I love doing it but it will always be reflected in the price. If I just factored my time into all the stuff I have offered, I would guess I am making pennies an hour. Right now, I have to have between and 6-7 trikes sold to make back the money that I have invested in this project. Again that's ok for me. Its a passion for me, but I can’t afford to lose money either. My full time job covers my living but not much after it.
Now I'm going make an educated guess on how this may affect what is happening in the prices of Lees items. First is the casting. I have a feeling that the price break down of his casts are similar to mine. I guess that he is paying not only for each cast but also the cost of material. Some of the prices I hear around the board that individuals charge is between $10-$30 for a head. I would guess he is paying the high side of that or even higher just for some of his heads. There is no question the quality of his castings are the best in the business. So every part that makes up a piece is going to cost money. If its the Plainview shotgun for example, its made of what looks to me to be 7 parts. Now the cost of material is low, but the caster still needs to make a mold for each piece and then also go through the labor of casting them. So a simple gun could get expensive just in the casting process. I know Danny is made of several pieces. The arms and the head at least are separate so there is four for Danny. They are also bigger sections then say the gun, so I’m sure the factory will charge a lot more in not only resin, but also the rubber for the mold. The body, I'll bet, is a real high priced part to make even though it’s probably a simpler than any of the other parts. So if we look at the cost of the body of Danny and compare it to a HT Truetype, I will bet it costs more to make Danny than Jack in terms of just the body. Also Lee had to sculpt the whole thing which, unlike a Truetype, takes a lot of time that he needs to charge for. If we then look at Danny’s costume you'll see that there are several parts. The overalls, sweater, and then the shirt. Im guessing that most of the cost that is associated with a scale costume comes from the labor of making and not the material used. With that rational. the costume for Danny, wouldn’t cost that much less than say Jack because it still is made of several parts. It also could be that the price is a little higher because its smaller and takes greater skill to assemble. I know from doing my own tailoring that the small stuff is harder. And then finally the head has to be painted. And the same rationale could made about painting. Size doesn't necessarily determine the price.
And my final guess is that Lee does this for a living. He is a professional sculptor and this is what he does to support his family like some of the other board members.
Now should all of these things I listed determine if a collector buys a really expensive doll? No. You buy what you like and pass on what you don’t. But maybe after this you can appreciate the amount of work and money that goes into this art form. Its not cheap to make and so it won’t be cheap to buy.
Well that turned out to be longer than I had thought. Oh well.
I have been working on this trike for about 6 months. I stopped paying attention months ago in the amount of hours. Lets just say a lot. The trick for these kinds of projects is there is often little reference. So for me I start going to period research in hopes to fill in the gaps where the movie still leaves off. This takes a lot of time on its own. Then there is the wonderful trick of taking measurements from the few images that you find so that the proportions can be addressed. I was taking measurements from the stills of Danny and his Mom walking so I could then cross reference to internet information about how tall the actors are. So that I then could determine what the height of the trike might be. I say might, because as you can imagine it all comes down to a guess in the end. Lee wanted the trike so he could then build the figure from it so I had to be sure and get as close as possible. I wanted to make sure these were as detailed and accurate as possible.
Once that is done the actual modeling happens. I opted to use a 3D CAD model because I knew that the objects printed would be more accurate in the end. Lee is brilliant at sculpting things by hand but I am no where near his level of perfection. I started it early on and found the wheel treads impossible to keep consistent. And I figured if I could do the wheels, I could do everything. I also knew that if I was going to ever come close to producing a large number in a short time, there was no way I could fabricate them by hand. This is where the price starts to be affected. If I was going to outsource everything it would make my production time shorter but the out of pocket price would skyrocket. That is why the gurneys are about the same price as these are because I don't have to worry about money paid out just labor. And trust me, I am making about 5 cents an hour for my labor on those. But its ok on those because that was the price I set. But it also has the affect of taking almost two years to finish. Just the metal parts cost nearly half of the price just to have them made and I haven't even added in the production of the plastic parts.
The most of the plastic parts have the luxury of being printed once and then cast but even they come with a per model price. I spent I think $375 for the prints of the plastic parts. The initial price is high because I wanted to get the absolute highest quality because I knew I was going to mold and cast them. Originally I was just going to print everything and avoid the casting costs but the quality for that amount was just too low so I opted this way instead. But the bell is going to be printed for each trike. The reproduction was just going to be too difficult. So the cost of each bell for the trike is little over $10 each. And that is getting a great deal from my printer. The first one was $20. The molding and casting of stuff can get pricey. Its not really affected by size for me, but more the amount of pieces. But I'm sure something like a figure would be much higher in price than the say the pedals. But even still every piece needs to be planned out and tested because to get the best cast, some trial and error has to happen. Im sure Lee’s cast are from a factory, because his castings a perfect. You can see the difference from say me and other board member’s head castings and one of his.
There is one section I was hoping to avoid fabricating but in the end, technology couldn't do it. I think its the main reason Lee wanted me to join him on this project because he could have easily made all the other parts. The frikkn front wheel. I had several different versions attempt printing it which cost me lots to have made, but in the end. it just couldn't be made that way. So I will be fabricating all the spokes and assembling each wheel by hand. The colored trike that Lee has for the prototype took me over 2 hours to make. I think I have the process figured out but still those are going to take some time. If the 30 Lee asked for have to be made, you can do the math and see what that will be like for me.
So as a wrap up, the collectors today expect this kind of attention to detail for this hobby. And I love doing it but it will always be reflected in the price. If I just factored my time into all the stuff I have offered, I would guess I am making pennies an hour. Right now, I have to have between and 6-7 trikes sold to make back the money that I have invested in this project. Again that's ok for me. Its a passion for me, but I can’t afford to lose money either. My full time job covers my living but not much after it.
Now I'm going make an educated guess on how this may affect what is happening in the prices of Lees items. First is the casting. I have a feeling that the price break down of his casts are similar to mine. I guess that he is paying not only for each cast but also the cost of material. Some of the prices I hear around the board that individuals charge is between $10-$30 for a head. I would guess he is paying the high side of that or even higher just for some of his heads. There is no question the quality of his castings are the best in the business. So every part that makes up a piece is going to cost money. If its the Plainview shotgun for example, its made of what looks to me to be 7 parts. Now the cost of material is low, but the caster still needs to make a mold for each piece and then also go through the labor of casting them. So a simple gun could get expensive just in the casting process. I know Danny is made of several pieces. The arms and the head at least are separate so there is four for Danny. They are also bigger sections then say the gun, so I’m sure the factory will charge a lot more in not only resin, but also the rubber for the mold. The body, I'll bet, is a real high priced part to make even though it’s probably a simpler than any of the other parts. So if we look at the cost of the body of Danny and compare it to a HT Truetype, I will bet it costs more to make Danny than Jack in terms of just the body. Also Lee had to sculpt the whole thing which, unlike a Truetype, takes a lot of time that he needs to charge for. If we then look at Danny’s costume you'll see that there are several parts. The overalls, sweater, and then the shirt. Im guessing that most of the cost that is associated with a scale costume comes from the labor of making and not the material used. With that rational. the costume for Danny, wouldn’t cost that much less than say Jack because it still is made of several parts. It also could be that the price is a little higher because its smaller and takes greater skill to assemble. I know from doing my own tailoring that the small stuff is harder. And then finally the head has to be painted. And the same rationale could made about painting. Size doesn't necessarily determine the price.
And my final guess is that Lee does this for a living. He is a professional sculptor and this is what he does to support his family like some of the other board members.
Now should all of these things I listed determine if a collector buys a really expensive doll? No. You buy what you like and pass on what you don’t. But maybe after this you can appreciate the amount of work and money that goes into this art form. Its not cheap to make and so it won’t be cheap to buy.
Well that turned out to be longer than I had thought. Oh well.
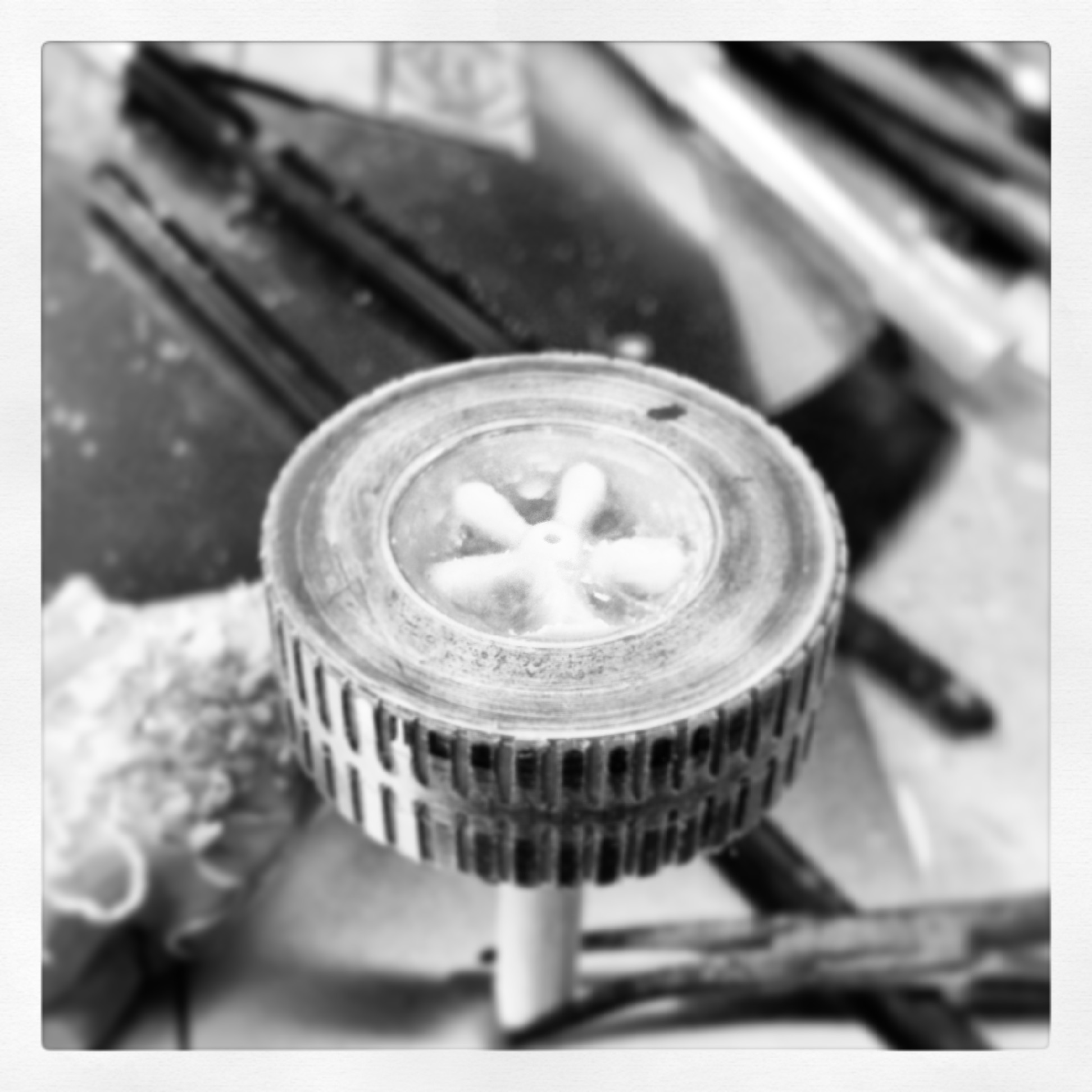
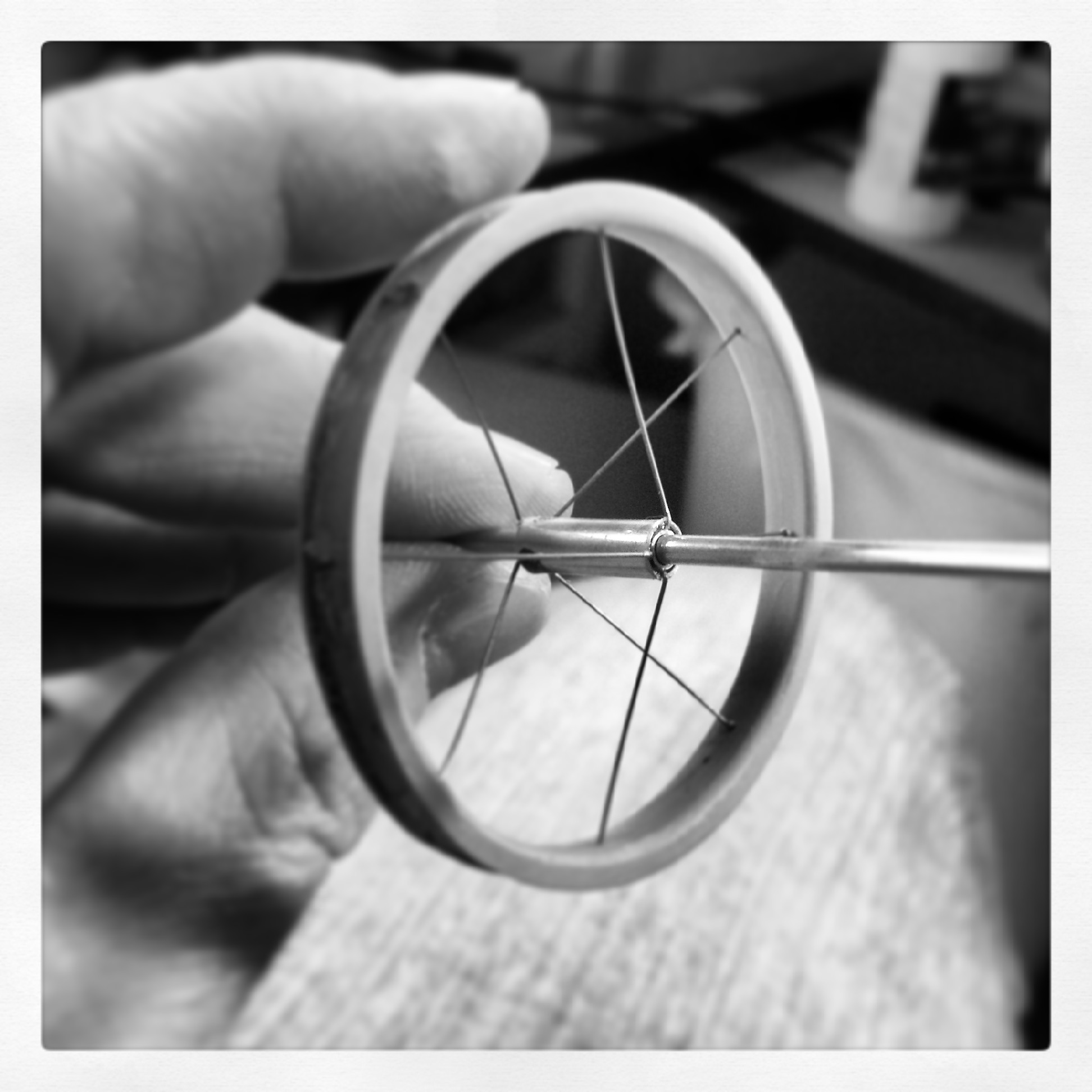
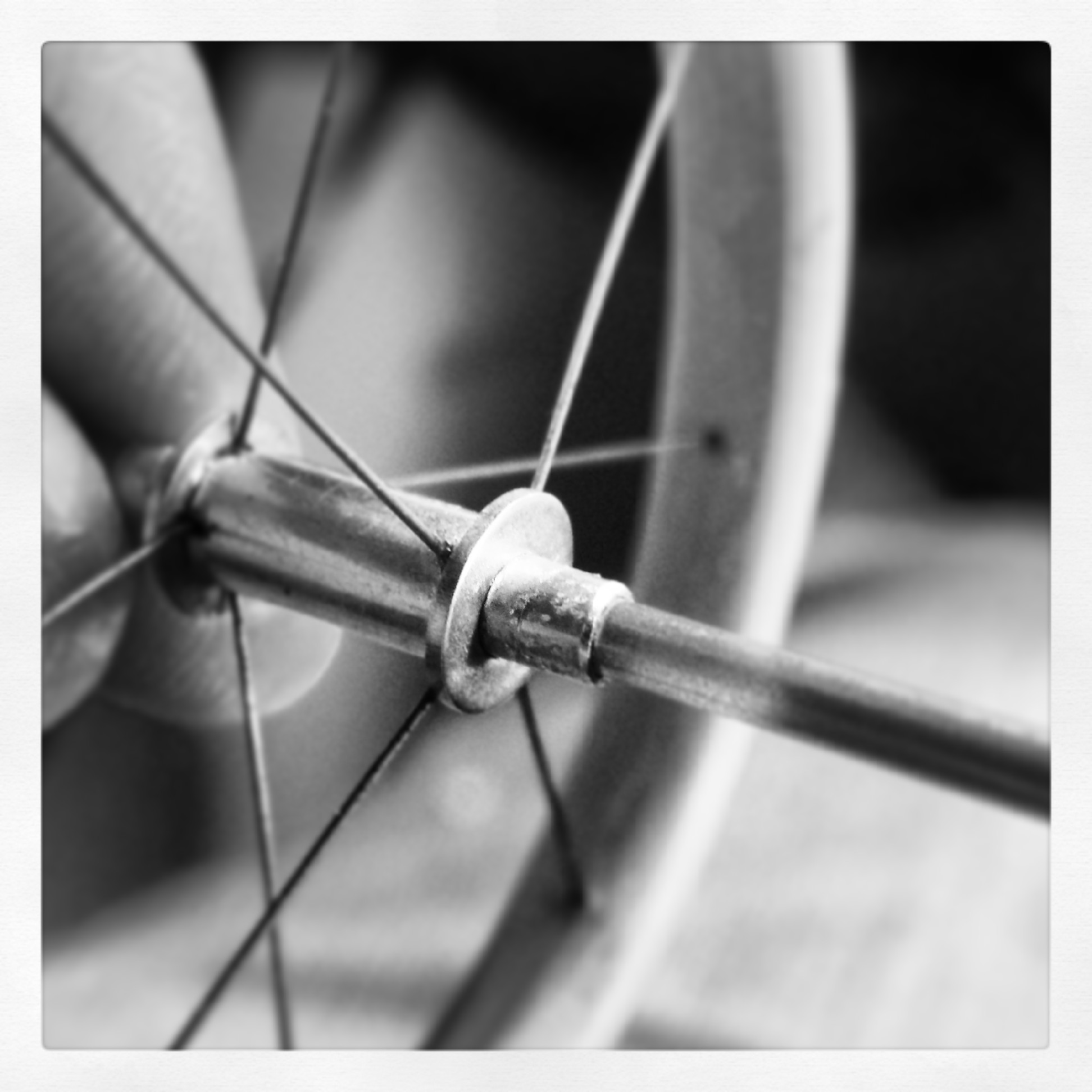
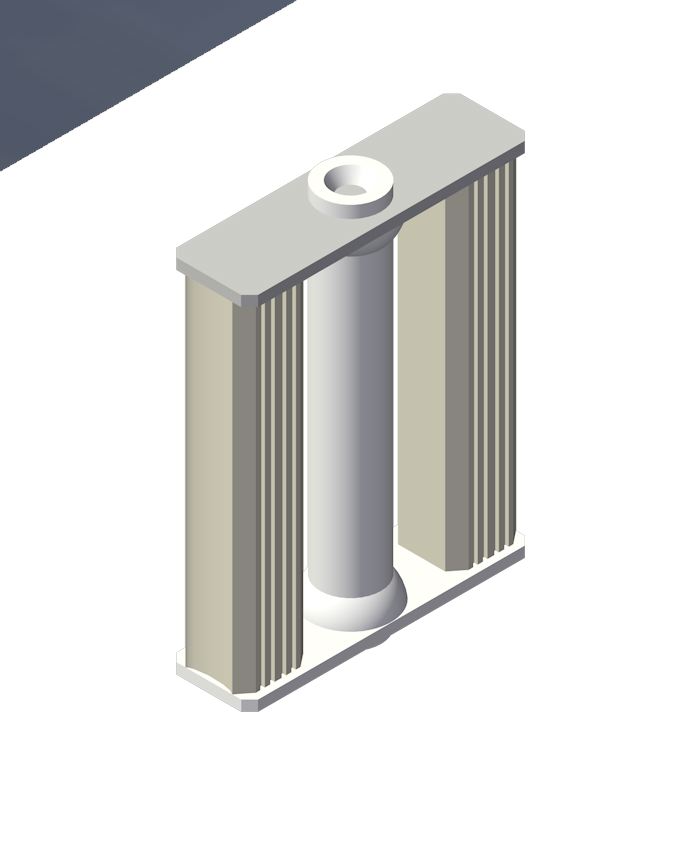
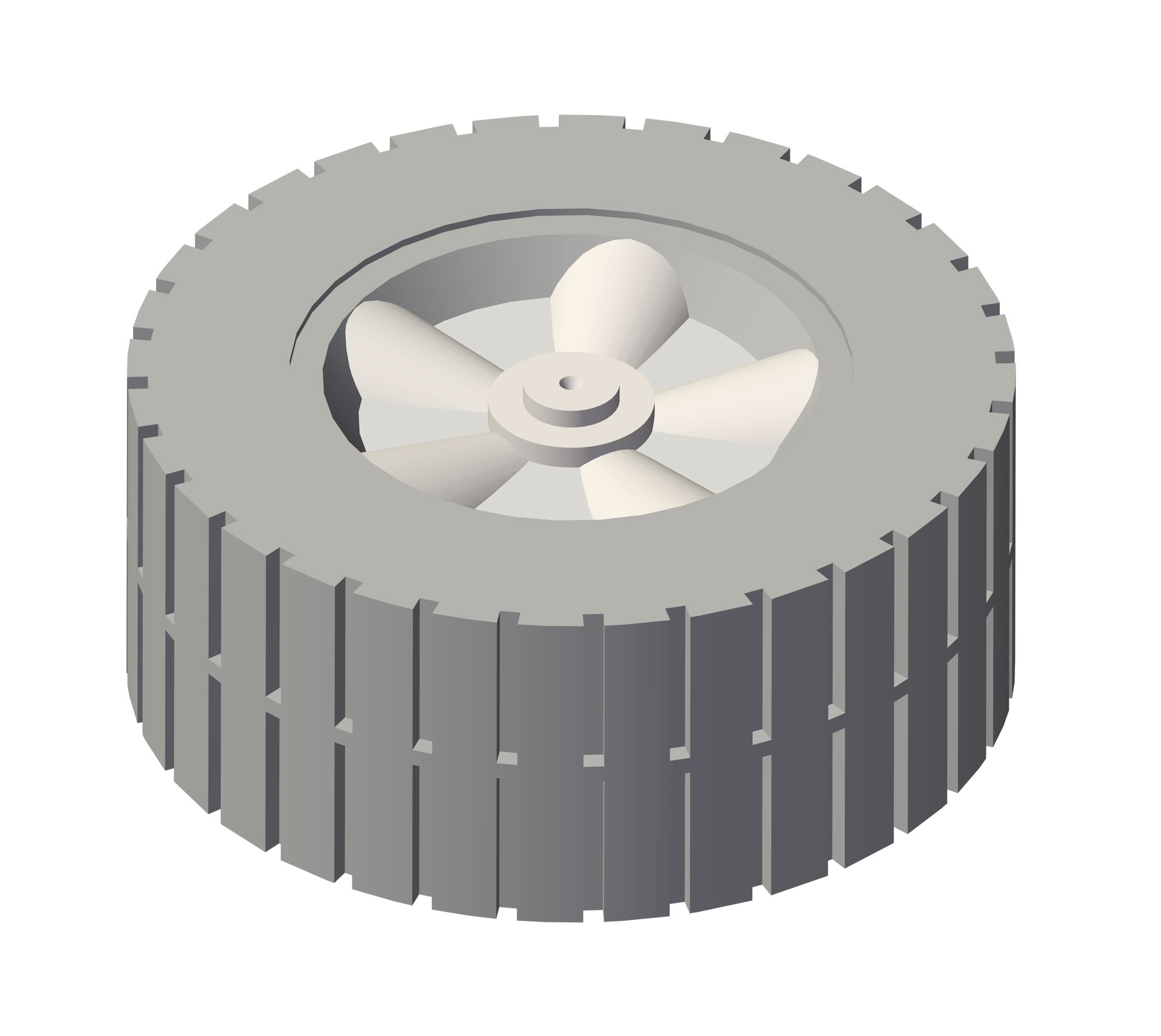
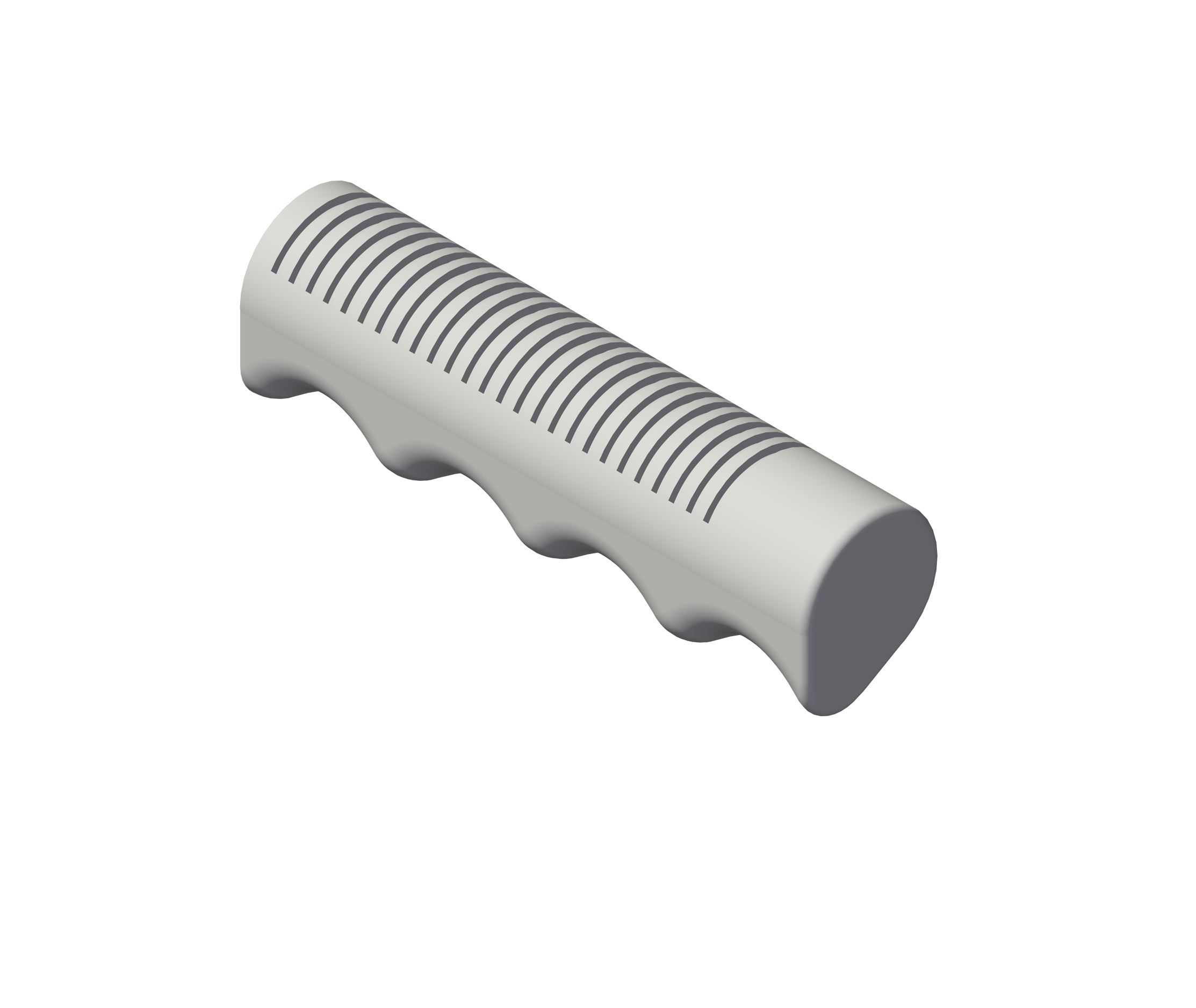
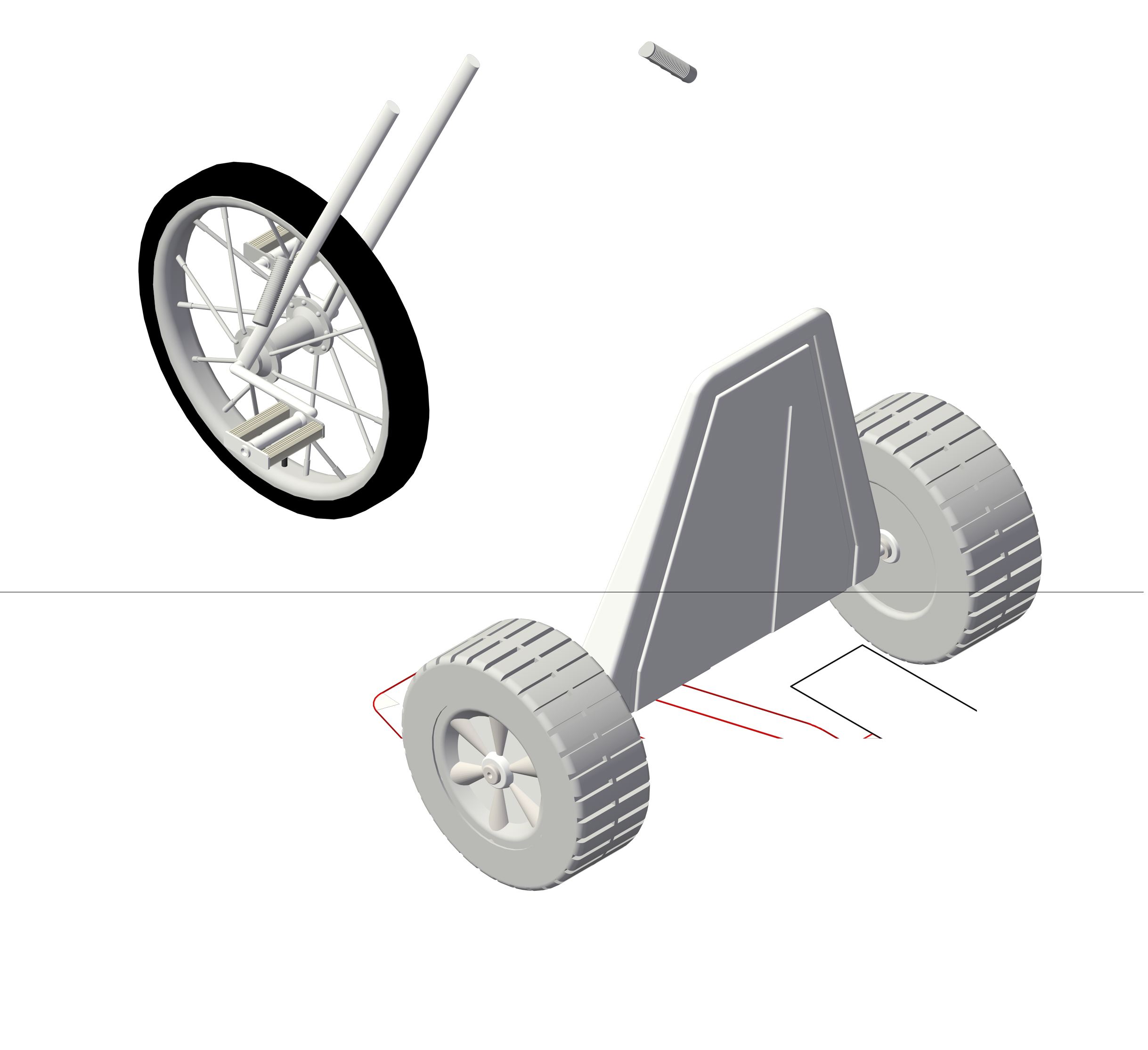
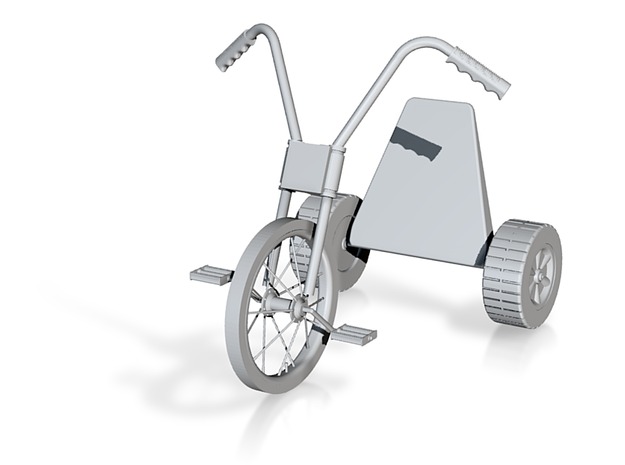
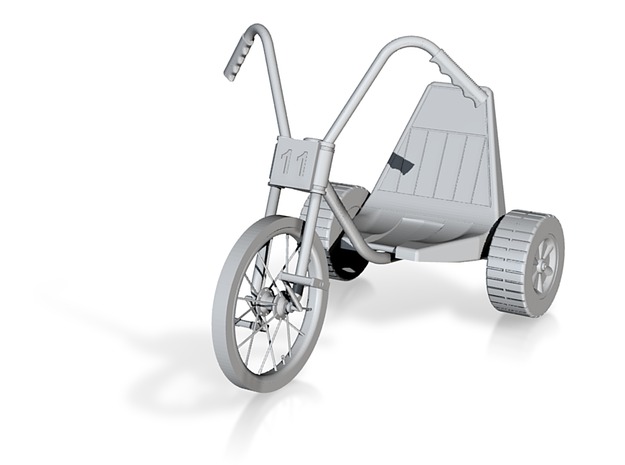
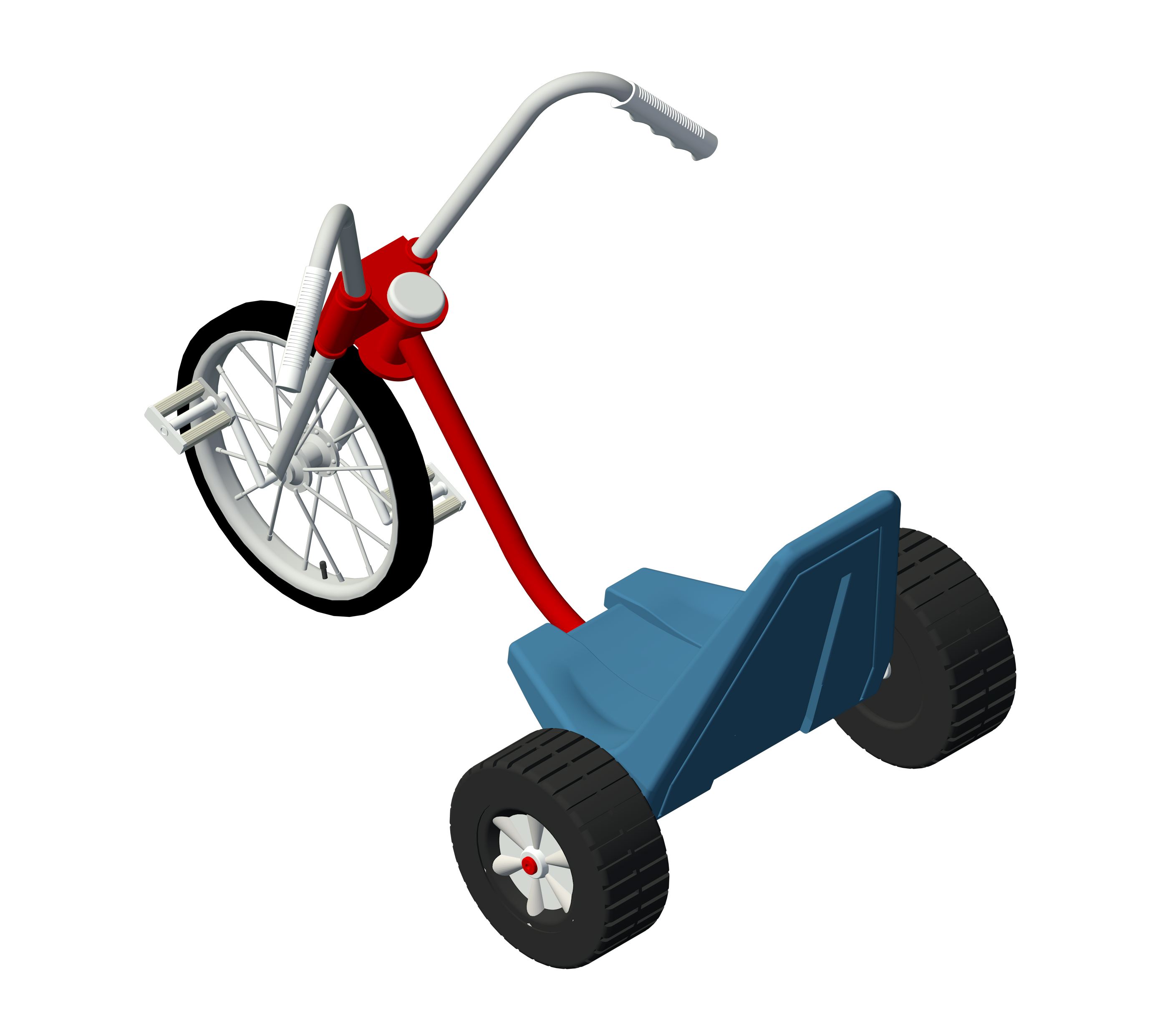
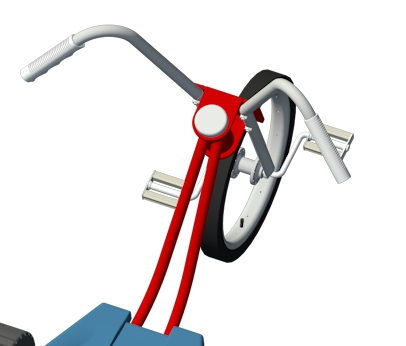