Marine Boy
Super Freak
Added the rear interior panels and cross bracing. Next step is the roll cage.
Exterior door handles made. These will be functional.
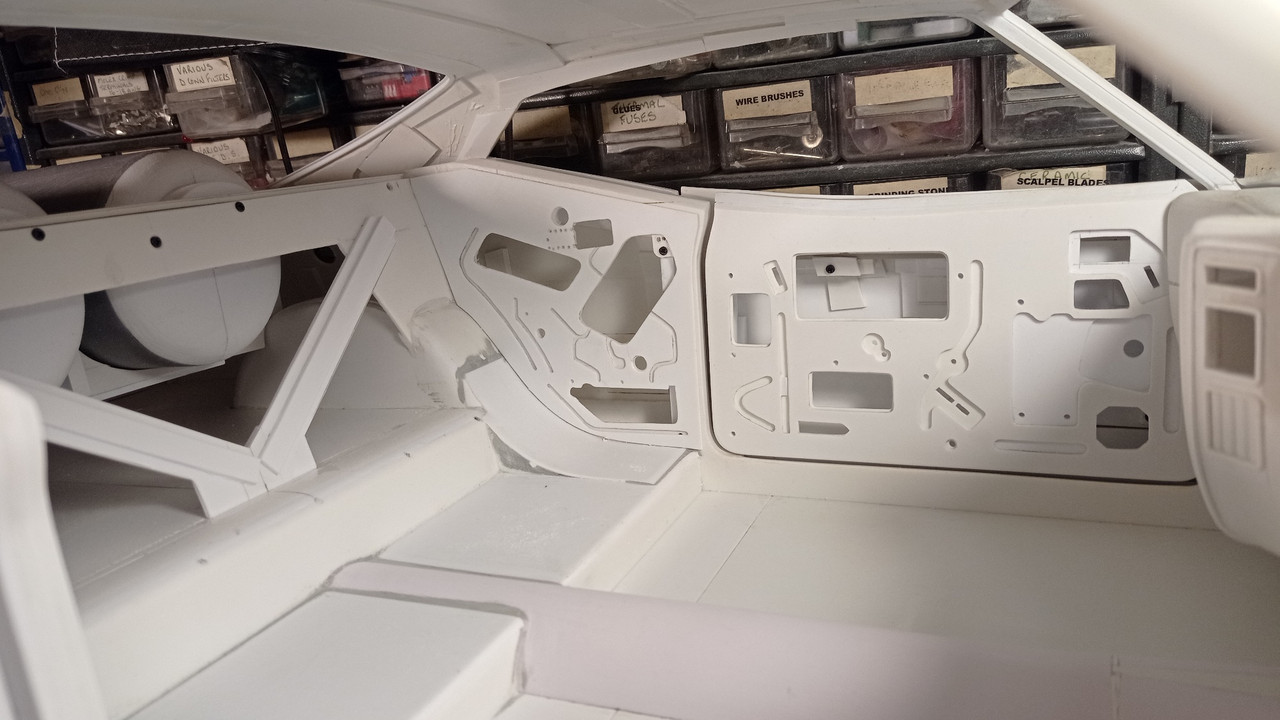
Exterior door handles made. These will be functional.
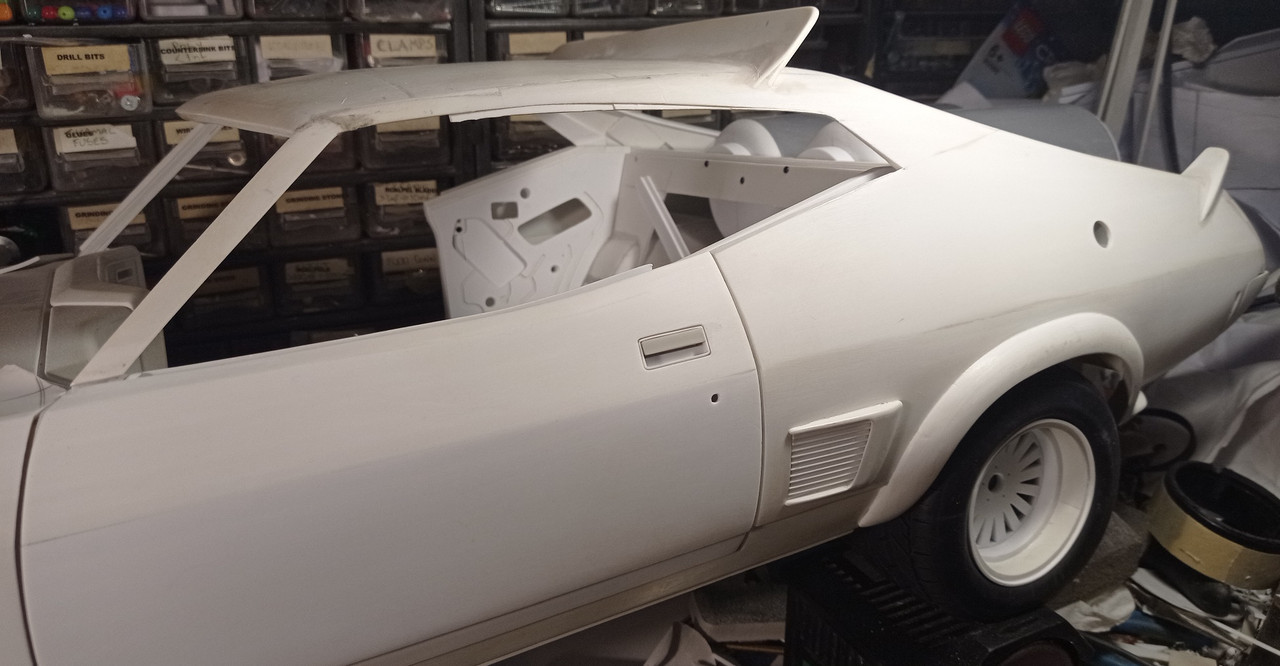
Last edited:
Enter your email address to join: